Known as "the teeth of industry",tungsten carbide have occupied an important position because of its outstanding wear resistance, strength, elastic modulus,as well as good corrosion resistance and other excellent properties, the application of cemented carbide has expanded from metal cutting tools to oil drilling, mining engineering, electronic communications and many other fields.
At present, cemented carbide is mainly produced by powder metallurgy, that is, firstly mixing and grinding raw material powder, then pressing and forming the blank parts , then sintering and densifying into cemented carbide parts, and finally grinding or polishing the sintered carbide to obtain finished carbide according to specified requirements. Although the method is mature and stable, and is used for large-scale production, it is only suitable for preparing products with relatively simple shapes and structures.
The emergence of 3D printing technology provides a solution for the manufacture of complex special-shaped cemented carbide products. At present, the study methods mainly include: selective laser melting(slm) ,selective laser sintering(sls),laserengineered net shaping based on high-energy beams(lens); extrusion-based fused filament fabrication(fff),direct ink writing(diw) and jet-based binder jet printing(bjp),etc.
But many problems occured too during the development. E.g:
- slm/sls/lens and other methods not only require high performance of raw material powder,under the irradiation of high-energy beam, the medium wc phase is extremely volatile carbon is transformed into w2c and resulting in impure phase in the printing process.
- The surface quality of the cemented carbide printed by extrusion-based diw and fff is poor, there are detailed interlayer traces, and there are discontinuous large holes and scattered small holes in the local area.
It is not difficult for experienced person who are familiar with the bjp to find that the degreasing, sintering process and post-processing process required by bjp is consistent with the process of the cemented carbide workpiece manufactured by the traditional injection molding process.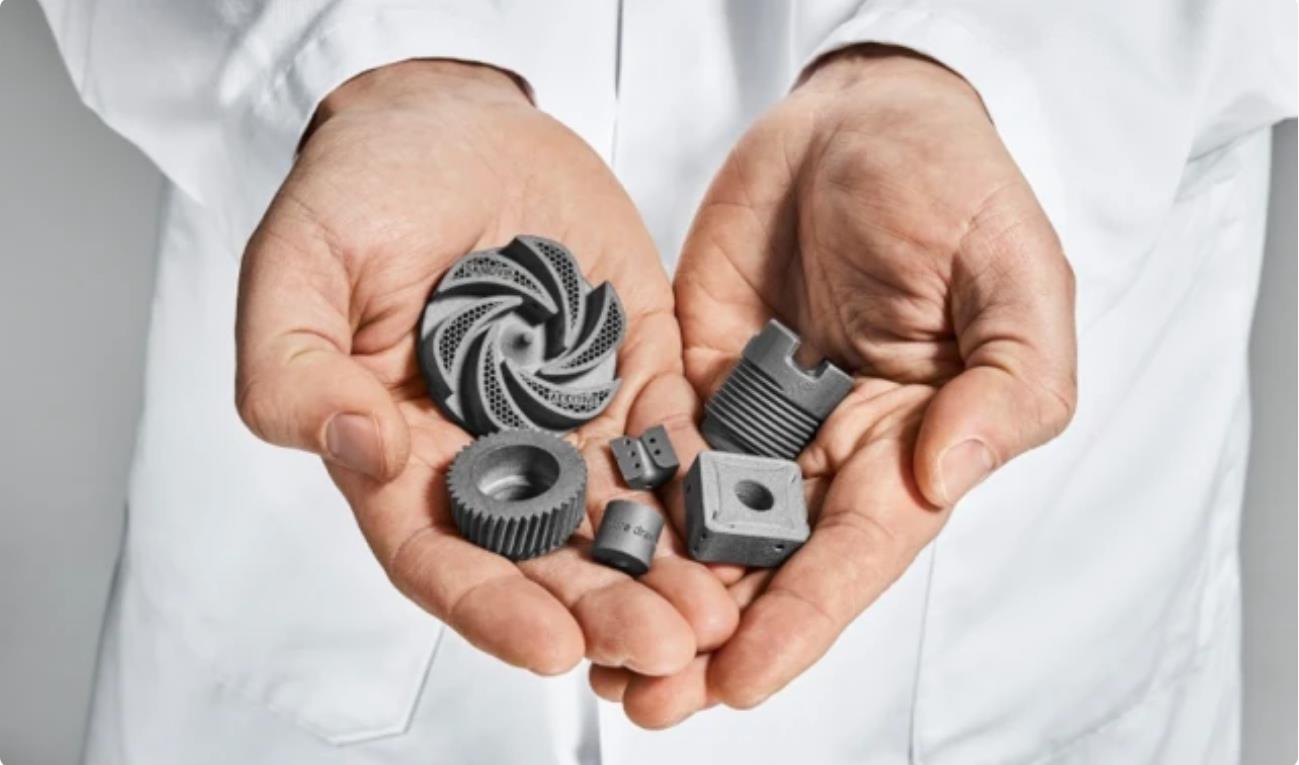
So thinking according to this logic, can Binder jetting metal 3D printing technology replace metal injection molding process or powder metallurgy process, and achieve cemented carbide workpieces that do not require molds and have more complex internal structures?The answer is yes obviously,TECNALIA from Spain uses its scientific research knowledge to help companies achieve greater success with disruptive binder jetting technology.Binder jet manufacturing overcomes the limitations of additive manufacturing processes that require support and can be used to machine desired but difficult-to-machine hard metals and tool steels. Design freedom enables performance-enhancing cooling channels to be integrated directly into the design middle.
In this case, the ExOne Innovent machine's flexibility to customize parameter settings, combined with the TECNALIA team's process and material expertise to customize properties for the application, has resulted in a breakthrough, delivering a final part with the desired properties. After sintering, carbide parts with densities comparable to conventionally manufactured parts are obtained. In addition, the hardness and fracture toughness of the material are also comparable.
Another company, MAPAL, has also used 3D printing technology to create a complex spiral cooling channel for the QTD series of tools, thereby improving the heat transfer ability of the coolant during the flow of the coolant to the top of the drill. MAPAL's drills last longer and run faster than previous drills.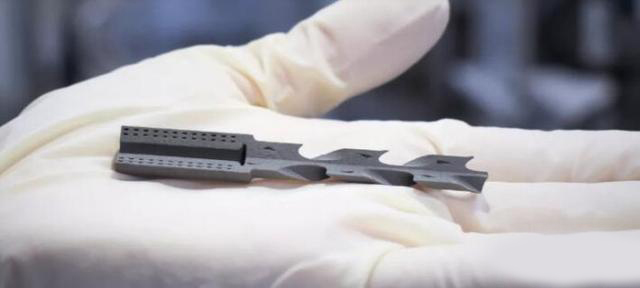
Another 3D printing technology, LPBF, is also frequently used in the manufacture of tools. Komet also used LPBF metal 3D printing technology and machining technology for the manufacture of milling cutters. The body part of the milling cutter with dense flutes is a customized non-standard product manufactured by metal 3D printing technology, and the shank part is a standard product mass-produced by machining technology.
Whether 3D pringting technology is used in the manufacture of carbide tools or LPBF technology is used in the manufacture of metal tool heads and tool holders, 3D printing technology occupies an increasingly important position in the manufacture of tools.